Building Regulations that Apply to Floors-Part J
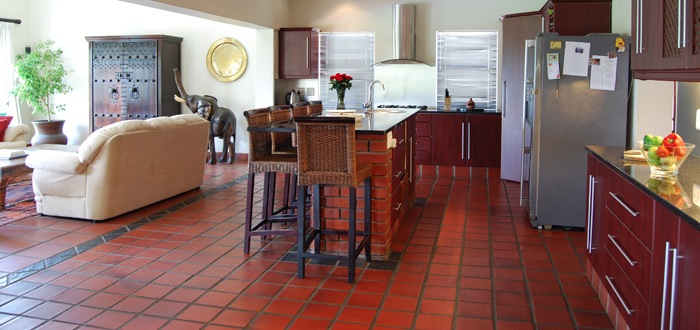
The Application of the National Building Regulations that apply to floors (Part J of SANS 10400) are certainly not exhaustive. In fact, if you think of how much of our house is floor, it’s what we might, in South Africa, describe as a biekie min. But the authorities have, at least, increased this part of the document from a single page to nine pages (although these include a page of references to other SANS that need to be taken into account, and more than a page of definitions) plus a cover page, a Foreword, Contents page, an Annex that gives the official, legal Regulations (see below), a one-line Bibliography – on a full page, a couple of blank pages and some info about the SABS Standards Division.
Changes to the Law
Like all the other parts of SANS 10400, Part J, Floors, has two sections. One section covers the Regulations (the National Building Regulations and Building Standards Act, 1977 and all its amendments) and the other covers how they should be applied (previously what fell under the “deemed-to-satisfy” rules).
In terms of the Regulations (the law), there is one substantial change to the first general requirement that previously stated that any floor of a building must simply “be strong enough to safely supports its own weight and any loads to which it is likely to be subjected”. It now states that “any floor of any building shall be designed and constructed to safely support its owns weight and any actions which can reasonably be expected to occur and in such a manner that any local damage (including cracking), deformation or vibration do not compromise the efficient use of the building or the functioning of equipment supported by such a floor”.
>
In addition (and this hasn’t changed):
- Floors must be fire resistant and where necessary, non-combustible.
- Floors of laundries, kitchens, shower-rooms, bathrooms and toilets (hooray, they are no longer referred to as WCs!) and urinals must be water resistant.
- Timber floors must have adequate under-floor ventilation.
- Concrete floors supported on ground or filling must be constructed in such a way that moisture will not penetrate the floor slab.
As always, the Regulations state that these requirements will be “deemed to be satisfied” if the design and construction of the floor complies with this part of SANS 10400. However, if the local authority deems it necessary, certain other requirements may be needed. For instance the local authority may demand that the entire area within the foundation walls of any building be covered by a suitable damp-proof membrane, and in the case of a basement, or semi-basement, they may require adequate sub-soil drains to be provided under the floor to drain and therefore remove any water that accumulates.
Interestingly, the Regulations now define the word “adequate” in this context:
a) in the opinion of any local authority
b) in relation to any document issued by the council, in the opinion of the council
So if you’re not sure of anything that relates to floors and flooring, approach your local authority for guidance. They are obliged to help you.
Application of the National Building Regulations
as they Apply to Floors
In addition to a number of SANS that relate to building materials including boards, timber, concrete and fire testing of materials, the SANS states that Parts A (general principles), B (structural design), H (foundations), T (fire protection) and V (space heating) of SANS 10400 must also be taken into account when constructing floors.
The Application of the Regulations relate to:
- floors in wet areas as specified in the Act (that must be water resistant)
- suspended timber floors that are not exposed to the elements
- floors and slabs supported on the ground
- all timber used for building
There are some useful drawings that show how suspended timber floors should be built.

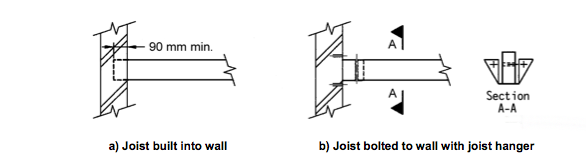
There are also specifications for maximum spans of floor joists:
- for those made with sawn SA pine for single- and double-storey houses
- for those made with laminated SA pine, Grade 5 or higher, also for single- and double-storey houses
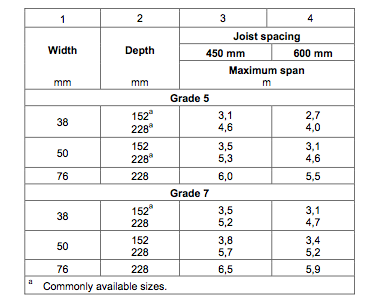
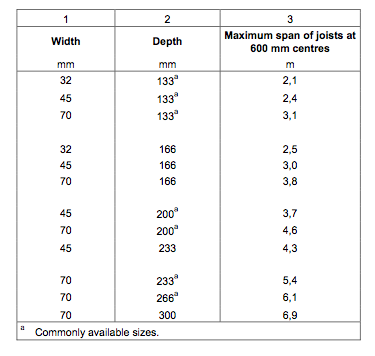
Additional floor specifications relate to:
- Flooring boards that must comply with SANS 629 and amongst other things should have a face-side width of at least 50 mm and not more than 140 mm, and tongued on one edge and grooved on the other, with square-sqwn or end-matched ends; and have tongues and grooves that produce a tight-sliding fit, and a flush joint on the face-side of the boards.
- Strip flooring that amongst other things should have a width between 35 mm and 90 mm and a nominal length of at least 460 mm (and tongues and grooves as above).
- Particle board that should comply with SANS 50312 and SANS 1931.
- Composite and plywood that should comply with SANS 929.
Additional guidelines relating to suspended wooden floors relate to the clearance between the joints and ground; ventilation; metal masonry anchors to be used and so on.
There are also a number of guidelines given for floors that are supported on ground or filling, but it is also stated that this type of floor should be designed and constructed in accordance with the requirements of SANS 10109-1 under the direction of a competent person (civil engineering) unless the building is to be used for storage or industrial purposes, in which case different guidelines are given.
This section also gives guidelines for underfloor membranes and filling beneath floors. Apart from anything else, a competent person (civil engineering) “shall design and inspect fills where the maximum height of fill beneath floors, measured at any point, exceeds 400 mm”.
So even if you go the DIY route, you’re going to need professional assistance.
>
Is a builder permitted to construct a a first floor slab with concrete beams and polystyrene blocks? Does this sound right?
There are various methods that builders use with concrete beams. I will write an article about these methods and let you know when it is uploaded.
What is the best sizes of joints between ceramic tiles? i have been looking through the national regulation book and cant find anything on it.
5mm or 10mm?
This is not governed by any form of regulation! It depends on the effect you want to create, and just how regular the tiles are. Generally wall tiles have a smaller grout joint than floor tiles. Rule of thumb is probably 10 mm for floor tiles and 5 mm for wall tiles. Spacers are good for maintaining a 5 mm-joint when tiling walls.
Hi there,
is there anything against having polished concrete floors though out the home?
Regards
Brent
There is no legislation Brent, but polished concrete can get very slippery if it gets wet. It’s probably a better idea to use a matt finish to seal concrete.
awesome.
Thanks for the suggestion, makes sense.
Thanks
I need help with the following questions:
1. What is generally used for floors and walls in operating theatres/laboratories in hospitals?
2. Is there any regulation/legislation one should be aware of with regards to flooring/walls in these areas?
3. The influence of cleaning and infection control in hospitals? Importance/will it affect choice of floors/walls?
4. Who specifies interior building products such as walls and floors in both private and public hospitals?
Tendani my area of expertise is domestic, although the National Building Regulations do cover all types of buildings including hospitals. Part J covers Floors and Park K covers Walls, but the requirements are really quite general. I am sure that there must be some other very specific national standards that relate to flooring and walls in hospitals. I suggest you contact the SABS to find out which ones might be relevant.
Hi. Do you know where in the Regs does it specify the width of a painted walkway in a factory?
Also, how wide must the painted line be?
Thanks
No Lindie, that isn’t specified in the building regulations. I think that painted factory walkways would fall under the Occupational Health and Safety Regulations.
hi there. in the design of floor slabs i would like a confirmation on the following.
1. on a 76mm fl.slab at 30mpa the steel indicated by the main contractor (which are a mining concern with no civil expertees.) ref 193 mesh. that could be done ?
2. the cover from the bottom is 50mm std for the mine.?
ive been in the construction for a lot of years and to my knowledge there is something out of standard.
my concern is that in the outside temp of 35C + the floor will crack up.
the total pour will be 700m/sqr in one go. hand floated. if the floor cracks up the responsibillity of the damage becomes mine. i need some back up, not to say any names but bldg regulations no so or so.
thank u JDV.
I suggest you contact the Concrete Manufacturers Association – click here for their link. I have found them to be incredibly helpful.
Halo just need to ask a question about industrial concrete floors in malls and shopping centres. What is a class 1 class 2 class 3 concrete floor and the maximum and minimum tolerance of the concrete finish level and the method of casting and floating?
Albert, Finishes to concrete floors is covered by SANS 10109-2.
The standard classifies recommended finishes in terms of abrasion resistance:
Class 1 (50 MPa) is for very high abrasion including steel wheel traffic and impact (heavy-duty industrial, commercial etc workshops); Class 2 (40 MPa) is high abrasion including steel or hard plastic wheel traffic (medium-duty); Class 3 (30 MPa) is moderate abrasion for rubber-tyred traffic (light-duty). There is also a “special” class for severe abrasion and impact.
Finishing processes for these are all trowelling twice or more (the higher the need for resistance to abrasion, the more number of trowelling operations will be required). Where a high resistance to wear is required, the finish should be floated after it has been spread, compacted and screened to level. Bull-, wood-, and power-floating are all acceptable methods. Further, floating and trowelling may be carried out mechanically or by hand.
The SANS classifies maximum tolerances in surface flatness as measured with a straight edge supported at two points 3 m apart. Where a high degree of accuracy is required (usually for a thin finish), the max tolerance = 3 mm. Where a low degree of tolerance is required (for thicker finishes or where regularity is not an issue) the max tolerance = 10 mm. A medium degree of accuracy = 5 mm max tolerance.
Note that this SANS is a 52-page document and it contains all the information you are likely to need. It is available from the SABS HERE for R240.
According to the Cement & Concrete Institute (C&CI) Class 1 is suitable for floors that require minimum irregularity (i.e. where you are seeking perfection); Class 2 is suitable for most construction work; Class 3 is suitable for floors where regularity is not an issue.
The C&CI has produced a very useful leaflet that you can download from our sister web site http://ownerbuilding.co.za/document-downloads/, for free. It is called Sand Cement Floor Screeds (scroll through the list) and provides information that is intended for architects, engineers and contractors who are specifying and laying floor screeds and toppings – to ensure that they are of the required quality.
It deals with specifying tolerances and various finishes, including floating, but not in as much detail as SANS 10109-2.
The C&CI also states that when it comes to the highest standard of surface regularity (Class 1), it may be necessary to use additional methods to finish the surface. They suggest a Concrete Society (UK) publication which you can also download from our Owner Building website. It is called Concrete Industrial Ground Floors.
Hi,
Can you advise what the minimum requirements (depth, waterproofing, etc) are for a garage concrete floor above a residential flat below.
Problem is that there was an oil spill in the garage that took a month before detection, and although now clean, there is a concern oil may leak through to the flat below.
What is the maximum deflection ratio for a timber floor where the floor is the first floor of a double story house? Has this chenged since 2008?
The wooden beams span 4 meters.
Hi Miles,
This is a question that an engineer (“competent person”) would have to answer, as there are many factors that have a bearing on the answer such as size and class of timber used, the load it is intended to support etc etc.
I can’t give you anything more specific than the general requirements. And how will you be able to check this now? It’s anybody’s guess whether it will leak! Sorry I can’t be more helpful Don.
I want to know what regulations in South Africa govern the
installation of an exterior door in a building with particular
reference to the required “step” between the interior and exterior of
the house at a doorway.
I recently bought a holiday home (Wooden Cabin) and the inside flooring is falling apart. Is there any regulations on how wooden flooring should be installed? The timber is joined in mid air and not on the support beams and I have already stepped through one.
I would like to take this up with the seller, since it was not disclosed to me during the sale and since I didn’t know better, I did not ask.
Any structure that is to be used as a “home” or dwelling requires approved plans. And yes there are regulations the specify how flooring should be installed. These include maximum spans for floor joists (depending on the timber used) and the timber used for floorboards. Most cabins (if I am imagining the correct type of structure) are supported on ground or fill – rather than on a solid foundation. In this instance, Part J of SANS 10400 state that the floor must be designed and constructed in accordance with the requirements of SANS 10109-1 and under the direction of a competent person (civil engineering). And it doesn’t end there. There are also regulations in terms of the ground or fill that the structure can be built on.
It is not clear whether you simply bought the cabin or a property that had the cabin on it. Either way you are probably covered by the Consumer Protection Act.
Thanks Penny.
The house was built in 2005. I bought the property with the cabin on it as the main dwelling.
I have spoken to a building contractor in the mean time and the estimated cost to replace the floors is in the region of R250K.
The contractor also confirmed my worst fears, the supporting beams are too far apart and the tongue and groove floor boards uses are too thin for pine.
He is also not too sure about the job, since the walls of the cabin was built on top of the floor construction?
I have contacted the NHBRC to get their opinion and will see my attorney next week.
Lijan, I have added to this page so you can get more of an idea what the NBR cover in terms of floors. The NHBRC manuals also have guidelines for floors, but unless the contractor who constructed the building was registered with them (which is highly unlikely because then they would have inspected the building several times during construction), they are unlikely to be very helpful. You would probably do better to approach the local authority, because it would have been their building inspector who approved construction at various points – unless of course the structure is illegal and was built without plans.
I presume that the walls are timber? You would probably need to have the entire floor removed – leaving the sections under the walls. Then you might need additional plinths – or posts – and a proper system of beams. Once these are in place, attaching the tongue-and-groove flooring is not a big deal.
You might want to get your money back and get out of the deal – though as soon as attorneys get involved, you will probably end up parting with most of the money their way. Good luck – let us know what happens.
Hi Penny
I have gone over all the purchase documentation and was stunned to see a clause that nullifies my rights to the CPA? I did not sign the option that gave me the right to the CPA conditions and was crossed out?!?
However, part of the Bank’s requirements for approval of my bond was a certificate of compliance to SABS 082. I do not have the full document, but I know that it contains the specification on wooden flooring.
I have contacted an attorney that specializes in the construction industry and am awaiting his feedback.
Thank you so much for your assistance!
Lijan
Hi Lijan,
Are you saying that the clause was crossed out but you did not initial it? If this is the case, you did not agree and therefore you do have rights to the CPA.
SABS 082 is an “old” regulation. SANS 10082, Timber frame buildings was published in October 2007 and supersedes SABS 082:1988 (second revision). I suggest you visit your nearest SABS office and have a look at the document – better, still, purchase a copy from the SABS – It costs R329. If there is no certificate of compliance – then surely they won’t pay out?
Good luck. Let us know what happens.
Julien, any steps or stairs must comply with Part M of SANS 10400 (Stairways).
For a single step, the important elements are:
1. The rise of any step shall not exceed 200 mm.
2. The going and width of any tread shall be not less than 250 mm, provided that where the stairway does not have solid risers, each tread shall overlap the next lower tread by not less than 25 mm.
There are drawings on the page I have given as a link.
Hi,
What will the law say about tiling of floors and walls? And how many shower and toilets for 20 persons?
There’s no law as such Willie, only SA National Standards (SANS) that govern things like how tiles are made. The way tiles are laid has to do with good building practice and not “the law”.
There are however safety aspects that must be followed – e.g. floors should not be slippery – and you will find these requirements in the building regulations under Part D, Public safety and in the Occupational Health and Safety Act.
In terms of the number of showers and toilets required, this depends on the type of building occupancy that is specified in General principles and requirements. I have recently replied to the same question at least twice. Have a look at these links – scroll down to Seelen’s query & Elizabeth’s query. They should give you more information.
Very nice blog post. I certainly love this website. Keep writing!
Hi.
I live in a flat which is 80 yrs old.wooden floors on beam
My question is,can I remove the wooden floors n screed to
Level n then tile
Thanx
Hi Richard,
It’s not clear from your description if you are on the ground floor or not. If you are on the ground floor then the “crawlspace” (the open space between the natural ground level and the beams) will need to be filled in and compacted before your damp-proofing, reinforcing and concrete floor is placed. This is not a small DIY job. As it is a block of flats then you will have to get approval from your body corporate first. If you are not on the ground level then it all depends on how the building was constructed. Many older buildings did not have concrete floors separating them. I would advise you getting an engineer in to inspect and let him/her decide if this can be done.
Hi,
We have a floor (first floor) of rib and block, the builder has placed a concrete stairway from ground floor going 90 degrees to top floor. The height from step to ceiling on the third step is only 180 cm, therefor will not pass building regulation. My question is that when I cut a piece of the upper floor away, can I then use square steel tubing to support the above floor, and if so can I fix it from the third step to the ceiling (most likely place to put it), and lastly what is the thickness of steel that I must use?
Thanks in anticipation.
Regards
Lewis
Hi Lewis,
This sounds too complicated and risky to ask and to answer in a post such as this. I suggest that you contact an engineer or another “competent person” to give you on site advice as this sort of fix needs to be done wtih the safety of all users in mind.
hi there
What is the requirements to build a woodern floor the maxium distance between beams
thank you
Gareth all the information given in the NBR relating to suspended wooden floors – including spacing of joists (which are the beams) – is in the article on this page.
Hi,
Please could you advise what the regulation is with regards to having an allowance between the internal and external floor levels. I’ve been told it needs to be 150mm, but this seems a bit excessive.
I have been told my 30mm height is not up to building regulations.
Thanks
Dean
Could you please advise me on the legal requirement for a wooden floor in a double story dwelling. There are two separate families living on either level.
Subject:
Concrete Floor Alignment
Message:
Hi
I have just purchased a brand new two bedroom apartment and a garage,I paid cash for the Garage R55000. The garage was handed over as Voetstoets ,the flooring is concrete : rough raw finish , not skimmed straight and smooth as i expected to be.Hills and valleys on the floor
Is there any regulations regarding my complaint.
Christine the floor would need to be constructed as shown on this page for suspended wooden floors. I am assuming that the fact that two families live in the dwelling is a factor – probably due to noise. This is not covered by the National Building Regulations.
Rajen it depends what your contract states. If it was to be skimmed or screened so that it was smooth this should have been specified. However if it is really sub-standard then you might have recourse via the Consumer Protection Act.
Hi Dean, the regulations do say the the minimum height between the average surrounding ground level and the top of the internal floor slab is 150mm. Normally you would not have a 150mm step down through a doorway. There should be a landing or patio that leads out through the door then a step or steps down.
Hi there.
I purchased a brand new flat from a develloper. After 14 months the tiles started coming loose and the grout falling out. The developer states that he has a 6 month warranty and after this time takes no responsibilities for defects. Is there some sort of law i can use to make him fix the tiles without me having to pay for the damage?
This is clearly a case of shoddy workmanship, however I don’t there is much that you can do except name and shame the developer – e.g. on Hellopeter.
I want to buuld a 2nd storey … not sue if I should go wood or concrete…. what is best …. and can I build the 2nd floor with wood what would be the consequence in s.africa
Hi Patrick, If you want to build a second storey on a single story house then the first thing you will have to find out is how strong your foundations are and if they can take the weight of a second storey. Timber is a much lighter material and many houses have a second storey built with timber. The timber materials have to be specified by a “competent person” and approved by council.
Hello,
What are the regulations regarding wooden flooring and Air Bricks/Ventilation?
Should all houses with wood flooring have air bricks or some type of ventilation?
In the National Building Regulations themselves it states:
“Any suspended timber floor in a building shall be provided with adequate under-floor ventilation.”
SANS 10400, Part J Floors (which is the SABS “deemed to satisfy” regs) states:
“Ventilation of the subfloor space in suspended ground floors shall be provided by means of openings spaced not more than 2,4 m apart with at least one opening within 0,75 m of each corner. The total area of ventilation openings provided shall be not less than 1 000 mm2 of unobstructed air passage per square metre of floor area. All ventilation openings shall be fitted with corrosion- resistant screening of nominal aperture that does not exceed 1,2 mm.
NOTE A 0,220 m × 0,170 m airbrick has an unobstructed area of between 0,006 m2 and 0,009 m2. Accordingly, one such airbrick is required to serve between 6 m2 and 9 m2 of flooring.
“Floor joists in suspended ground floors shall be set on and skew-nailed to sole plates that have minimum dimensions of 38 mm × 76 mm on top of sleeper walls (see figure 2). Sleeper walls shall be provided with sufficient openings to ensure good cross ventilation.
NOTE At the junction of solid and suspended floors, e.g. at verandahs, ventilation pipes might have to be provided underneath solid concrete floors. Where sleeper walls are used, ventilation openings of size at least 115 mm × 75 mm spaced at 1,0 m centres should be provided.”
Hi, I live in Pretoria and I removed the joists which upheld the wooden floor above my basement. The basement and the room above now have a concrete roof/ floor. I would like to re- use the original pine wood planks over the concrete slab instead of tiling. I’m told that solid wood must be placed on top of wooden strips that are nailed into the concrete yo prevent rotting and promote circulation of moisture. Could you please provide your technical suggestions or recommends in this regard? Many thanks, Fatima
Fatima if you look at Part J of SANS 10400 – some of which is covered in the link I have given you – you will see that there is a section for Floors supported on ground or filling – that gives some information. Wood though is not mentioned specifically and the method you mention isn’t either. If you Google “wooden flooring on concrete” you’ll see there are various ways including something similar to what you describe but using “sleepers’ underneath which I presume would be quite hefty – and they would need to be to carry the weight of the wood. You could probably also screed the concrete with mortar to which a waterproofing compound has been added and then paint with bitumen and/or use a DPC and then place the wood on top. A problem with sleepers/strips etc is that these affect the height of the ceiling from the floor. BTW I presume you are talking about using the “wood planks” (floorboards) that were originally fixed to the joists. Many modern wood and simulated wood products are manufactured to be attached directly to a screened (so it is smooth) concrete surface. Sorry I can’t be of more help.
Hi, What constitutes as a “Basement”? Is there a certain percentage of the space that needs to be below “Natural ground level”? Or as per the building regulations, is it just a space below ground floor? If so, then what qualifies as the “Ground floor”?
I am designing a parking space that is mostly underground, would that count as a basement level?
Thanks!
Marnus, presumably if you are designing a “parking space” you are a competent person and therefore know or have access to this information. The only advice I can give comes from the definition of “storey” in the NBR:
a) the ground storey shall be taken as the storey in which there is situated an entrance to the building from the level of the adjoining ground or, if there is more than one such storey the lower or lowest of these,
b) a basement shall be taken to be any part of the building which is below the level of the ground storey,
d) the height expressed in storeys shall be taken to be that number of storeys which includes all storeys other than a basement
You will find the full definition in Part A of SANS 10400.
Do plans have to be submitted to local municipalities for the partial enclosure of a patio?
Keith if you are using a solid building material e.g. bricks and mortar or even timber-frame, your local authority is likely to require plans. There is also the issue of classification or use of the area. This needs to be specified on the plans. But the municipality has the authority to either call for plans or decide that it is “minor building work“, in which case plans won’t be needed.
Hi, we’ve build a second storey with timber and it wasnt done by qulified builders, however they have years of experience.
We having endless problems with the shower, with water running down to the ground level. I’ve had several plumbers in to fix the problem that created more problems on the ground level. Now we have cealings that need to be replaced everytime it happens. We’ve stopped using the shower due to the fact that we cant find someone that knows what they doing. Advise please.
Good day, I am extending my house by 40 sqaures, just an extra room and en suite. On the plan it says the exterior wall should be 280mm, which means it should have a gap of 50mm between inner and outer bricks. When I checked after thd builders were done, the gap is only10mm. They have laid the foundation concrete and juat built up a couple of courses, the slab has not been laid yet. Could they still build the cavity wall with 50mm gap from the slab upwards or must the same gap / cavity be from the very first course all the way to roof height?
Hi id like to know in a project whose responsibility is it to do levels or finish floor levels between the architect and the engineer..??
Hello
What are the regulations regarding garage floor with an integral door to the rest of the house? I seem to think it needs to be 150mm below but would it serve the same purpose if it were 150mm ABOVE the house floor. It is an old house and the ground level outside is the same as the floor into the house – there is no step into the front entrance.
Many thanks.
there are no regulations stating that a garage floor must be higher or lower than the rest of the house. The regulations for Foundations Part-H say that the outside ground level must be a minimum of 150mm below the DPC (Damp Proof Course). The DPC is the plastic waterproofing strip that is built into the wall between the foundation and the brick wall.
The gap in the foundation walls usually gets filled with cement/mortar or concrete and then the walls above the slab should have a minimum 50mm cavity and be built with wall ties evenly spaced throughout.
What is the cost of using timber vs concrete to floor the second storey
That is called homework and you have to phone the timber and concrete suppliers and get prices from them and then compare for yourself, we do not do quotations etc, sorry.
Is this correct? I am under the impression that a garage floor must be at least 80mm below the floor level of the house where there is direct access from the garage to the house. As for “oil stores” this prevents burning oil etc. from entering the house. Maybe the by-laws differ between the municipalities.
What is the right mix for screed in a public toilet?
It really doesn’t matter where you are laying the screed. A suitable mix would be 130 litres of concrete sand for each 50 kg of cement + enough water to produce a nice, workable consistence.
Pierre neither Part H: Foundations nor Part J: Floors of SANS 10400 mention garages. Garages are mentioned in Part T: Fire Protection. e.g. doors to any garage have to have a certain fire resistance. There is also a clause that relates to parking garages for more than 10 cars that states: “The floor of any occupancy classified as J4 shall be of non-combustible material and shall be not less than 10 mm lower than the threshold of any door leading to any adjoining room or space.”
There might be some sort of municipal by-law – your local authority will be able to advise.
First lesson: Always use qualified builders. Second lesson: Only qualified registered plumbers should be used – that’s the law. Third lesson: Go back to the first and second lessons and employ people fully qualified and equipped to do the job. Cutting corners is more costly than doing it right the first time.
It’s the builder’s responsibility to do the levels and finishes. It is the responsibility of the competent person (could be an architect or an engineer) and the local authority building inspector to check that these are done correctly.
we bought vinyl wooden floor and had it installed with under floor heating, within a month the vinyl started bubbling up, we called the company and told them to fix the floor, they uplifted the entire flooring and the heating, after several specialist coming to check, they realized that there is moisture underneath. now we need to know if we can force them to fix the floor, we have decided to put porcelain tiles instead, can we force them to buy the porcelain tiles and install as we have paid over R28000 for the vinyl and cannot really use it due to the moisture in the bedrooms. did they have the responsibility to check before installing that the floor was suitable for the wooden vinyl floor?
we do not want to pay again for the heating and the new floor, surely they must meet us halfway at least with the costs. please help
Hi Noni, Installation of finishes by a private company are not covered by the building regulations. This is a legal matter between yourself and the installers and you should consult an attorney ar there is a fair bit of money involved here. You could also contact one of the consumer bodies here: http://www.southafrica.info/services/consumer/consumer or you could consult a consumer complaints expert here : saconsumercomplaints
we are wanting to lay a 7m x 7m concrete slab separate to the house as a base for a braai area (No walls and no roof). There is no electrical or plumbing requirements. Are we required to have plans made for it?
I bought a house which was 5-6years old. About half the tiles in the living area sounded hollow to a tap; in some places the grout was breaking up as well. Tile tiles in other areas were fixed well eg on the stairs.I was advised to have all the tiles lifted and have the living area retiled. Though the tiles were quite thin (cheaper quality),about a third of the tiles lifted were not broken and had no chunks of cement sticking to the back.
Could you tell me why the tiles in a relatively new house can become loose like that?
Thanks for your help!
I have a house built by Garden Cities. My snag list had hollow tiles mentioned – numerous were located. I was told that hollow tiles were not a problem but should a problem arise in the future they would deal with it – unfortunately only verbal. 5 1/2 years later a large section of my open plan area has now lifted and the developer says its not their problem. Is there anything I can do?
Hi Uda, This is due to bad workmanship. This seems like the tiler skimped on tile adhesive and did not put adhesive over the full underside of the tile but used the 5 spot method – a spot of adhesive on the 4 corners and one in the middle leaving gaps in between. That is why you can hear hollow taps. This is never reccomended as the tiles can crack and lift over time.
Janec.
Thank you for coming back to me. The tiles that was lifted in one piece, had cement stripes/ markings on the back. The tiler must have “combed” the cement and then laid the tiles, not the spot method, but after about 5 years the cement just did not keep holding on to the tiles!? No chunks of cement stuck to the tiles.
Hi Uda, Well all I can say is that the tiler must have used really cheap tile adhesive. That is not right for them to lift after only 5 years.
Other than sue them, no. Never accept verbal assurances – and if you are worried about something get a second opinion. If the tiles sound hollow, they probably laid them using blobs of tile adhesive or mortar which is a common cause of tiles cracking. The entire under-surface of tiles must always be covered.
No
I am interested in epoxy flooring in general whether industrial or commercial will you guys help me in getting a training with regard to knowing how to do epoxy flooring I want to provide this services type of service.Please link me with a company or training institution that can help to acquire the skill please
Unfortunately we are not able to help. Plascon Paints has epoxy flooring products; perhaps they can help.